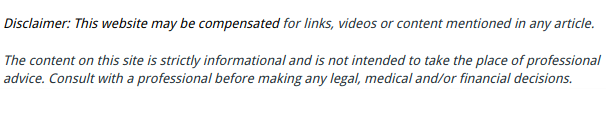
Compressed air is a vital utility in countless industries, powering everything from assembly lines to spray booths and pneumatic tools. A well-designed compressed air line piping system is essential to ensure that this vital resource is delivered efficiently, reliably, and safely across the facility. While often overlooked during planning stages, the layout and components of a compressed air piping system can significantly affect overall system performance, energy usage, and equipment lifespan.
Understanding the Role of Compressed Air Line Piping
Compressed air line piping systems serve as the distribution network that carries compressed air from the compressor to the various points of use within a facility. Much like a circulatory system, these lines must maintain sufficient pressure while minimizing drops, leaks, and moisture buildup.
A properly installed and maintained system ensures consistent airflow, protects sensitive equipment, and maximizes operational efficiency.
Materials Matter: Choosing the Right Piping
One of the most important decisions in designing a compressed air line piping system is selecting the appropriate material. The choice impacts not just installation and durability, but also long-term performance and maintenance. Common options include:
-
Aluminum: Lightweight, corrosion-resistant, and easy to modify, aluminum is an increasingly popular choice. Its smooth interior also reduces friction losses, helping maintain air pressure throughout the system.
-
Stainless Steel: Known for its strength and durability, stainless steel resists corrosion and withstands high pressure. It’s ideal for harsh environments or when contaminant-free air is critical.
-
Copper: Traditionally used in smaller systems, copper offers good corrosion resistance and is relatively easy to install. However, its use is less common in large-scale industrial applications.
-
Plastic (such as PE or PVC): While lightweight and easy to work with, not all plastics are suitable for compressed air systems due to pressure limitations and safety risks. Only materials rated for compressed air use should be considered.
Material selection should align with the demands of the application, the environment, and the level of maintenance anticipated over time.
Designing the Layout for Maximum Efficiency
The layout of a compressed air line piping system plays a significant role in maintaining performance and reliability. A poorly designed system can lead to excessive pressure drops, increased energy consumption, and uneven air distribution. To avoid these issues, consider the following design principles:
-
Loop Systems: A looped layout, where air can reach outlets from multiple directions, provides more consistent pressure and airflow. It also allows maintenance on sections of the system without interrupting overall operation.
-
Drop Lines: To supply air to specific tools or workstations, drop lines should be installed vertically, with takeoffs from the top of the main line to reduce moisture carryover.
-
Main Trunk Lines: Ensure the main lines are large enough to handle the total airflow. Undersized pipes create bottlenecks, increasing pressure drop and reducing efficiency.
Proper layout not only supports system performance but also improves accessibility for maintenance and minimizes future expansion challenges.
Moisture Control and Drainage
One of the common issues in compressed air line piping systems is moisture. As air compresses, water vapor condenses into liquid. If not managed properly, moisture can lead to rust, equipment damage, and reduced system performance.
To control moisture effectively:
-
Slope the Piping: Horizontal runs of piping should have a slight slope (typically 1 inch per 10 feet) to allow condensed water to flow toward designated drainage points.
-
Use Drip Legs and Drain Valves: Drip legs—vertical extensions with drain valves—should be installed at low points in the system to collect and remove water.
-
Install Aftercoolers and Dryers: These accessories remove moisture before the air enters the piping system, reducing the load on the piping and downstream filters.
Moisture management is critical for maintaining clean, dry air, especially in applications requiring high air quality.
Minimizing Pressure Drop
Pressure drop is the reduction in air pressure from the compressor to the point of use. Excessive drops result in underperforming tools, wasted energy, and increased wear on equipment.
Several strategies can help minimize pressure drop:
-
Choose Proper Pipe Sizes: Larger diameters reduce resistance and accommodate higher air volumes.
-
Avoid Sharp Bends and Excess Fittings: Every elbow, tee, and valve introduces resistance. Designing with gradual bends and minimal fittings helps maintain pressure.
-
Monitor and Maintain Filters: Clogged or dirty filters can choke airflow, increasing the pressure drop. Regular inspection and replacement are key.
Keeping the pressure drop low helps the system run more efficiently and reduces strain on compressors.
Expansion and Flexibility
As operations grow, compressed air needs may change. Designing a system with future expansion in mind prevents costly redesigns and downtime. Incorporate extra ports and accessible layout points for quick additions. Modular piping systems, especially aluminum and stainless steel varieties, allow for easier changes and additions.
Safety and Compliance
Safety is paramount when dealing with pressurized systems. Improper materials or installations can result in dangerous failures. All piping and fittings must be rated for compressed air use and installed according to the manufacturer’s specifications and local safety codes.
When designed and maintained with care, a compressed air line piping system becomes a quiet powerhouse, working behind the scenes to keep operations running smoothly. Whether for a small workshop or a large manufacturing plant, getting the piping system right is a foundational step toward peak performance.