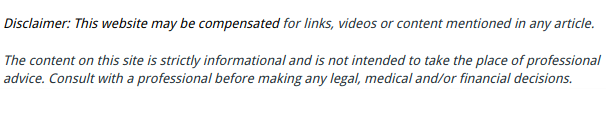
Custom sign manufacturing is an intricate process that involves a variety of steps from conceptualization to installation. Whether for businesses, communities, or personal projects, custom signs play an important role in communication and branding. This article delves into the frequently posed questions about custom sign manufacturing to unravel the details behind the craft.
What Are the Key Steps in Custom Sign Manufacturing?
Conceptual Design and Planning
The initial phase of custom sign manufacturing is the conceptual design and planning stage. This step involves close collaboration between the client and designers to ensure objectives are clearly defined.
How Neon Signs Are Made for Restaurants — How to Make It
By understanding the client’s aesthetic preferences and functional requirements, designers can create a precise vision of the final product.
During this stage, various design drafts may be produced and iterated upon based on client feedback. The use of cutting-edge software aids in visualizing the concepts before they’re brought to life. Effective communication is vital to ensure the final design aligns with the client’s vision and objectives.
Moreover, this stage emphasizes the importance of strategic planning. Designers take into account various factors such as the intended use, placement, and visibility of the sign. This comprehensive approach ensures the creation of a sign that effectively communicates the intended message while meeting all aesthetic goals.
Material Selection and Procurement
After finalizing the design, the next stage is selecting and procuring the materials needed for production. This step is crucial as it influences the durability, aesthetic appeal, and cost of the final product. Various materials such as metals, plastics, and composites may be considered, each offering unique benefits.
The selection process involves evaluating each material’s suitability for the intended use of the sign. Factors like weather resistance, color retention, and lighting compatibility are considered. It’s essential to choose materials that not only fit the budget but also withstand environmental conditions.
Once materials are chosen, procurement involves sourcing high-quality raw materials from reliable suppliers. Relationships with these suppliers are critical, as they ensure timely delivery and a continuous supply of materials. By prioritizing quality and reliability, manufacturers create signs that endure over time and continue to look appealing.
Fabrication and Production
In the fabrication and production phase, the design transforms from a concept into a tangible product. Advanced technologies such as CNC machines, lasers, and 3D printers are leveraged to ensure precision and consistency. Skilled artisans play a role in adding detailed craftsmanship that enhances each sign’s uniqueness.
This stage focuses on executing the design with meticulous attention to detail. Techniques like digital printing, cutting, molding, and assembling are used to bring each component together. The collaboration of technology and human skill results in high-quality, customized signs that reflect the design accurately.
Efficient production management is crucial to maintain timelines and quality control. The use of project management software ensures every step is monitored, from raw material usage to quality checks. Each sign undergoes rigorous testing for durability and appearance before it reaches the client, guaranteeing satisfaction.
How Long Does It Take to Manufacture a Custom Sign?
Initial Consultation and Design Phase
The timeline for custom sign manufacturing starts with the initial consultation and design phase. This period is dedicated to understanding the client’s needs, which informs the draft designs. The duration can vary, typically taking one to three weeks, depending on the complexity of the design and feedback loops.
During consultations, designers gather essential information such as the client’s goals, preferred styles, and budgetary constraints. The creation of design drafts provides a visual representation for client review. Iterations and approvals are conducted to refine the concept until it matches the client’s expectations.
Effective communication and collaboration often speed up this stage. A well-organized design phase ensures momentum is maintained throughout the manufacturing process. Investing time and effort here lays a strong foundation for a successful custom sign project.
Production Lead Time
Once the design is approved, the production lead time commences. This stage involves turning the approved design into the actual product, taking approximately two to four weeks on average. The time required is influenced by factors like the complexity of the design, the materials used, and current production schedules.
Manufacturers allocate resources efficiently to adhere to these timelines. Any complexity in the design could extend the timeframe due to the intricate crafting and technology needed. Nevertheless, using advanced equipment and experienced teams helps streamline the production process, ensuring quality and efficiency.
Regular communication between the manufacturer and client is maintained to set realistic expectations. Providing updates at various stages ensures transparency and allows clients to plan for eventual installation. By understanding the production lead time, clients can better anticipate when their custom sign will be completed.
Installation Scheduling and Timeframe
Installation is the final step in the custom sign manufacturing process that requires logistical planning. Scheduling this stage involves coordinating with the manufacturing team and the client to choose an optimal installation date. This can take from a few days to a week, influenced by the site’s complexity.
During this stage, experienced technicians ensure that the sign is properly installed, safely secured, and optimally positioned. The installation process is integral to the sign’s performance, requiring precision to avoid damage and ensure visibility. Weather conditions and site accessibility are also accounted for in scheduling.
Thorough preparation and site assessment are conducted to anticipate any potential challenges. This ensures a seamless installation process, minimizing disruptions and maximizing effectiveness. The installation phase concludes the manufacturing process, bringing the client’s vision to life with a high-quality, custom sign.
Understanding the process behind custom sign manufacturers can help consumers make informed decisions. When considering custom signage, weigh the time, costs, and materials involved while focusing on your specific needs and goals. Engaging with experienced professionals ensures a smooth process from conception to installation, resulting in a superior final product.