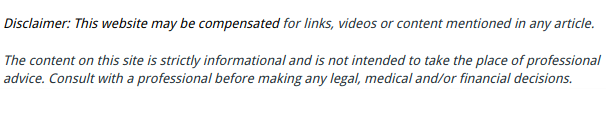
In this article, we will explore the differences between cogged Vbelts and standard Vbelts, two common types of transmission belts used in various applications. Understanding the distinctions can help in selecting the right belt for your needs, thus improving performance and longevity. Knowledge of these belts is crucial for engineers and technicians involved in machinery maintenance and design.
What Are the Primary Differences Between Cogged Vbelts and Standard Vbelts?
Design and Structure
One of the primary differences between cogged Vbelts and standard Vbelts is their design and structure. Cogged Vbelts feature indentations on the inner side, allowing them to be more flexible and efficient.
In contrast, standard Vbelts have a simpler, smoother design, which can limit flexibility but may be more suited for straightforward applications.
These structural differences influence how each type of belt performs in various scenarios. The cog design helps to reduce bending stress, enhancing durability and performance in challenging environments. However, the uniform design of standard Vbelts can be advantageous for applications requiring steady, uninterrupted force.
For industries that prioritize versatility and efficiency, the cogged belt’s intricate design provides substantial benefits. Its ability to conform to smaller pulley diameters without cracking under stress makes it ideal for compact machinery. In contrast, the standard V-belt suits non-variable or low-stress conditions, where durability and a lower price point prevail.
Performance in Various Applications
In terms of performance, cogged and standard Vbelts excel in distinct environments. Cogged Vbelts are known for their superior performance under high-load conditions due to their enhanced flexibility. The design facilitates improved heat dissipation, a critical factor in high-speed applications, ensuring sustained performance without the risk of overheating.
Standard Vbelts showcase reliability in uncomplicated settings where equipment operates at consistent speeds and loads. Their solid construction minimizes the potential for mechanical failure in less demanding applications. However, they might lack the adaptability required for more dynamic or varied operational settings.
Ultimately, the choice of belt type is contingent upon the application’s specific demands. Industries dealing with machinery that undergoes frequent speed variations or intense stress might pivot towards cogged Vbelts for improved efficiency. Conversely, equipment that maintains a routine operational pace could significantly benefit from the straightforward nature of standard Vbelts.
Durability and Maintenance Considerations
Durability is a pivotal consideration when choosing between cogged and standard Vbelts. Cogged Vbelts generally offer enhanced durability due to their flexibility and efficient stress distribution across the belt’s surface. This attribute not only extends their lifespan but also reduces the frequency of replacements, leading to cost savings over time.
When evaluating maintenance, cogged Vbelts demand slightly more attention due to their intricate design and precise installation requirements. Despite this, their superior grip and lower tension mean they require less frequent adjustments. Standard Vbelts, conversely, offer simplicity of maintenance, ideal for systems where downtime is detrimental.
Both belt types require regular inspections to ensure optimal performance. However, if an application cannot afford spikes in operational costs or intensive maintenance, the standard V-belt’s lower upkeep profile might be preferred. In contrast, the cogged V-belt’s potential for long-term savings in high-stress or critical applications may justify its more intricate care requirements.
When Should You Use a Cogged V-belt Over a Standard V-belt?
Ideal Situations and Conditions
Choosing between a cogged V-belt and a standard V-belt often depends on specific operating conditions. Cogged Vbelts are ideal in scenarios where machinery is subject to varying load conditions or requires rapid, frequent speed adjustments. Their flexibility and efficiency make them suitable for compact systems where traditional belts might struggle.
Environments that either produce excessive heat or involve high-speed operations demand the adaptability of cogged Vbelts. Their structure assists in heat dissipation, making them favorable over standard variants in such settings. This is especially pertinent in industries where overheating could significantly disrupt operations or damage equipment.
In contrast, under conditions of steady operation without major fluctuations in load or speed, standard Vbelts are often sufficient. They provide reliability and cost-effectiveness in scenarios with minimal mechanical strain. This makes them suitable for systems where precision and adaptability are secondary to straightforward, dependable performance.
Cost-Effectiveness and Efficiency
The decision to use a cogged V-belt often correlates with calculations of cost-effectiveness and efficiency. Initially, cogged Vbelts may seem more expensive due to their complex design and material engineering. However, their ability to enhance energy efficiency by reducing slippage can lead to long-term savings in power consumption.
In terms of maintenance, while standard Vbelts may necessitate fewer immediate expenditures, cogged versions generally require less frequent replacement. The balance of initial cost versus longevity and maintenance expenditures often tips the scales in favor of cogged belts in high-use scenarios. Industries that prioritize reduced operational costs may prefer cogged options to maximize resource allocation.
Efficiency gains from cogged Vbelts arise not only from reduced energy consumption but also from minimized downtime. Efficiency is increased due to their lower operational noise, which can benefit environments where noise pollution is a concern. Although the upfront cost of a cogged V-belt might be higher, its overall contribution to a leaner, more efficient operation frequently justifies the investment.
Summing up, we have explored the fundamental differences between cogged Vbelts and standard Vbelts. By choosing the right belt type for your machinery or equipment, you can enhance performance, reduce costs, and ensure longevity. Consider the factors discussed to make an informed choice for your specific application needs.
.